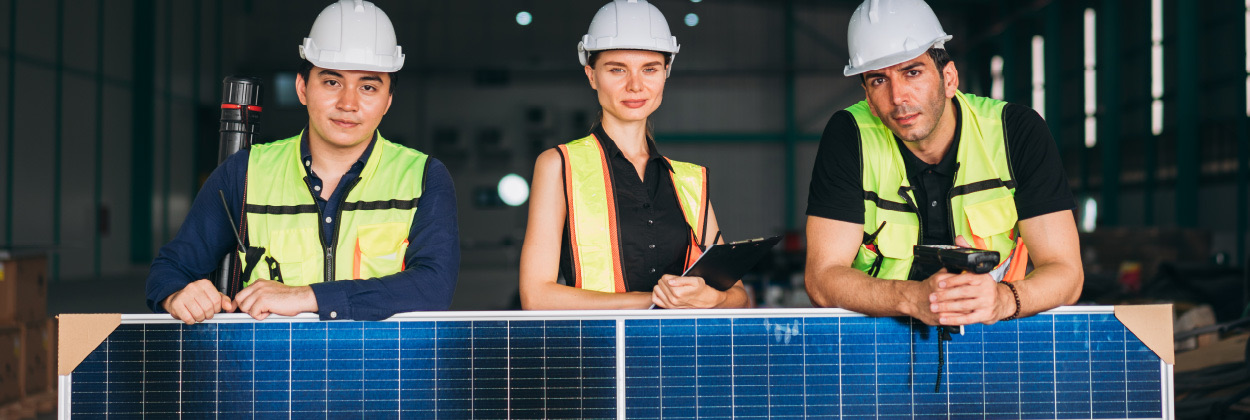
What Solar Panels Are Made Of and How They're Made
Ever wonder what's behind that shiny surface of a solar panel? Or how these silent energy producers are crafted? You're not alone. Solar panels, the unsung heroes of renewable energy, are fascinating pieces of technology.
In this article, we'll delve into the world of solar panels, unraveling the mystery of their composition and manufacturing process. We'll explore what materials are used, how they're assembled, and why it all matters in the grand scheme of sustainable energy.
Get ready to embark on a journey that'll illuminate the science behind these sun-powered marvels. It's a fascinating tale of innovation and sustainability, and it's all about to unfold.
Basic Components of Solar Panels
Dive deeper into the intricate world of solar panels, exploring the key components that fuel their power. Let's unpack the fundamental elements that form these impressive renewable energy powerhouses.
Photovoltaic (PV) Cells
At the heart of any solar panel, you'll find Photovoltaic (PV) cells. Playing a crucial role in the conversion process, the PV cells transform sunlight into electricity. Typically made from silicon, a semi-conductive material, these cells absorb photons from sunlight. The energy absorbed, in turn, causes electrons to move, creating an electric current. To optimize their function, PV cells usually come in two types: Monocrystalline and Polycrystalline. Monocrystalline cells use single crystal structure, bestowing them a slightly higher efficiency level and sleek appearance, while polycrystalline cells, deploy multiple crystals.
Remember, PV cells are the hardest working component in a solar panel, the energy transformers tasked with harnessing the power of the sun.
Glass and Encapsulation Layers
Once you move from the core PV cells, you'll encounter the glass and encapsulation layers. Protecting the solar cells is a tempered glass front layer, designed to withstand various weather conditions and ensure durability. This high-transparency glass layer allows maximum sunlight penetration, resulting in optimal energy harnessing capability.
Additionally, beneath the glass front is an encapsulation layer, typically made from ethylene-vinyl acetate (EVA). This layer secures the PV cells, preventing moisture and dirt ingress, thus ensuring a long lifespan for the solar panels.
Preserve these indispensable components, and your solar panel transforms the sun's rays into a powerful energy source. Get a grasp on these basic components, and you're one step closer to understanding solar panel functionality.
Materials Used in Solar Panels
Digging deeper into the makeup of solar panels, we find a variety of materials playing pivotal roles. These materials, each with unique properties, contribute to the superior efficiency and functionality of solar panels.
Silicon (Monocrystalline, Polycrystalline)
Most solar panels integrate the use of silicon, owing to its semiconducting characteristics. Similar to the way your body relies on the heart for survival, solar panels rely on silicon to convert sunlight into an electric current. Used in two chief forms, Monocrystalline and Polycrystalline, silicon forms the bulk of Photovoltaic (PV) cells. Here's how:
- Monocrystalline Silicon - Named so because it originates from a single crystal structure, Monocrystalline silicon offers high purity and efficiency. Its streamlined design, indicated by its rounded edges and deep black color, reduces the waste of silicon and aids better electron flow.
- Polycrystalline Silicon - Contrasting monocrystalline, polycrystalline silicon is produced from multiple crystals. It's efficiently priced, albeit less efficient in performance than its counterpart. Known for its distinctive blue hue, it's a common choice in areas where the cost is more pressing than efficiency.
Thin-Film Materials (Cadmium Telluride, CIGS)
Moving away from silicon-based solar cells, thin-film technology carries its unique set of materials. This technology excels in environments with less direct sunlight, providing a versatile alternative to traditional methods. Key players in thin-film materials include:
- Cadmium Telluride (CdTe) - This material offers an economical option compared to silicon, even though it's less efficient. Its main advantages lie in its cost-effective manufacturing process and shorter energy payback time.
- Copper Indium Gallium Selenide (CIGS) - Proving a worthy competitor with Silicon cells, CIGS offers higher efficiency ratings. Its complex manufacturing process, however, prompts a higher price tag compared to CdTe. The use of CIGS symbolizes a blend of efficiency and low-cost production, promising an exciting future for thin-film solar technology.
Each of these materials represents a piece in the grand puzzle of solar panels, contributing to the rise of sustainable energy solutions. They frame the intricate process by which a simple beam of sunlight transforms into a powerful energy resource.
Solar Panel Manufacturing Process
After understanding the key materials that compose a solar panel, let's delve into how these components come together in the manufacturing process. Here we'll take a detailed look at the creation of silicon wafers and the assembly of PV cells into panels.
Silicon Wafer Production
In solar panel manufacturing, the production of silicon wafers holds significance. These wafers serve as the primary platform for PV cells. Industrial-grade silicon undergoes a purification process, transforming it into poly-silicon. This poly-silicon is then melted and recrystallized to create single-crystal silicon, referred to as mono-silicon. Slicing this mono-silicon block into thin pieces generates the silicon wafers. Each of these wafers, thin yet durable, is well-equipped to capture and convert radiant sunlight into usable electricity.
Assembly of PV Cells into Panels
With the silicon wafers at hand, we move on to the assembly of PV cells into panels, a step vital to the construction of solar panels. From these wafers, manufacturers create PV cells. Employing an anti-reflective coating on these cells boosts their ability to absorb sunlight, not letting valuable energy merely bounce off. These cells, arranged in a precise matrix on a solar panel, create an electric field. When exposed to sunlight, the cells work in sync to convert the sun's light into electricity, bringing the panel to life. This streamlined assembly process maximizes the effectiveness, efficiency, and energy output of the solar panels.
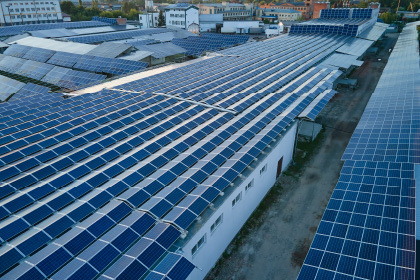
Delving further into the world of solar panels, you'll uncover an array of distinct technologies, each boasting unique characteristics and advantages.
Types of Solar Panel Technologies
Delving further into the world of solar panels, you'll uncover an array of distinct technologies, each boasting unique characteristics and advantages. Two broad categories dominate this realm: Crystalline Silicon panels (Monocrystalline and Polycrystalline) and Thin-Film panels, each contributing significantly to the modern solar landscape.
Monocrystalline vs. Polycrystalline Panels
Crystalline Silicon panels, as their name implies, primarily rely on silicon crystals in their design. These types of panels branch into two forms: Monocrystalline and Polycrystalline.
Monocrystalline panels offer superior efficiency rates due to the use of single, high-grade silicon crystals. These panels, characterized by their sleek, black aesthetic, typically possess an efficiency of 20% or more. For instance, a 300 sq ft area dedicated to Monocrystalline panels can produce up to 6 kilowatts of energy.
Conversely, Polycrystalline panels employ multiple silicon fragments fused together, leading to a slightly lower efficiency rate, albeit at a reduced cost. These panels, identifiable by their bluish hue, average efficiencies of 15-17%. Hence, a 300 sq ft area might generate around 5 kilowatts of power with Polycrystalline panels.
Thin-Film Panels
Moving away from Crystalline Silicon, we find Thin-Film panels, another remarkable branch in solar technology. These panels comprise several thin layers of semiconducting materials such as Cadmium Telluride or Copper Indium Gallium Selenide. Thin-Film panels are noted for their sleek design and lower cost, making them suitable for large-scale installations where space isn't a constraint.
Though Thin-Film panels may not match the overall efficiency of Crystalline Silicon panels, they present excellent performance in lower-light conditions. For instance, on an overcast day, a Thin-Film panel might perform more efficiently than its Crystalline Silicon counterparts.
Several types of solar panel technologies coexist, each with unique strengths and ideal use-cases. By understanding these details, informed decisions can be made to select the most suitable technology for individual solar panel applications.
Quality and Durability Considerations
When choosing a solar panel, its performance is vital, the durability and quality are equally critical. This section assesses those considerations-backed by reliable data-to help you make an informed choice.
Testing for Strength and Durability
Solar panels face numerous environmental elements like wind, hail, and heat. To withstand these conditions, manufacturers conduct stringent tests on their products. For instance, hail tests involve firing ice balls at the panels to mimic hailstorm conditions. On the other hand, the mechanical load test asserts a panel's capacity to endure the weight of snow or force of wind.
A vital indicator is the International Electrotechnical Commission's (IEC) certifications denoting a panel's standard. The IEC 61215 standard denotes that a solar panel has successfully passed tests for durability and weather resistance, ensuring it can handle prolonged exposure to the elements.
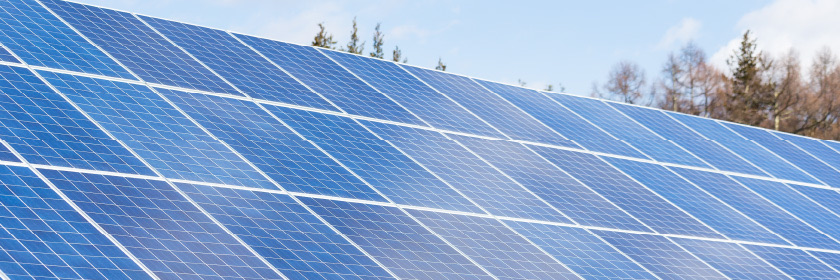
Ensuring Long-Term Performance
For a solar panel to be truly sustainable, its long-term performance is paramount. Wise customers examine aspects like the panel's degradation rate, which signifies the rate at which a panel's output decreases annually. Research by The National Renewable Energy Laboratory (NREL) shows that the median degradation rate for photovoltaic panels is around 0.5% per year for monocrystalline and 0.8% per year for polycrystalline. Thus, a well-made solar panel can retain 90% of its capacity even after 20 years.
Additionally, comprehensive warranty details highlight a manufacturer's confidence in their products' longevity. Typically, solar manufacturers offer two types of warranties: a product warranty and a performance warranty. The former guarantees against defects or issues in manufacturing for 10-12 years on average, while the latter ensures that the solar panels will produce a certain amount of electricity for 25-30 years. Decoding these warranties gives a glimpse into the possible long-term performance and expected life cycle of your chosen solar panel.
Environmental Impact of Manufacturing
Delving into the environmental footprint of solar panels, it's crucial to analyze two critical parameters: energy consumed during production and efficiency in waste management.
Energy Use in Production
In manufacturing solar panels, energy demand is a concern. Producing crystalline silicon panels, which make up a substantial part of solar energy systems in use today, requires significant energy. This involves the transformation of pure silicon into crystalline silicon, which is an energy-intensive process. Data indicating these energy requirements are significant. For instance, Journal of Cleaner Production records indicate the energy input during production is about 1,030 kWh/m², potentially resulting in high greenhouse gas (GHG) emissions. This element implies an extended energy payback time, signifying the duration a panel must operate to compensate for the energy consumed in its manufacture. This payback period ranges between 1 to 4 years, with Geoscience Australia estimating most payback periods to fall within 2 years.
Waste and Recycling Efforts
On the subject of end-of-life management for solar panels, there exists a significant challenge. Annually, tons of solar panels reach their end-of-life, translating into a considerable waste problem. The International Renewable Energy Agency estimates about 78 million metric tons of solar panel waste will mount up globally by 2050. Despite this daunting prospect, many solar manufacturers and institutions are launching recycling initiatives. Silicon-based materials of spent panels can be recovered for reuse, representing a recycling rate of about 96% by weight. Consequently, the industry is eyeing a circular economy concept, where upon reaching their end-of-life, materials from solar panels can be recovered and re-introduced into the production cycle. European Union directives, for instance, now mandate the collection and recycling of solar panel waste, exemplifying regulatory efforts to address this challenge.
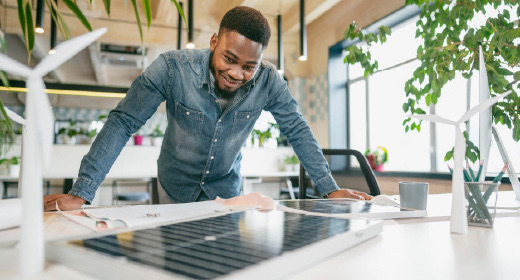
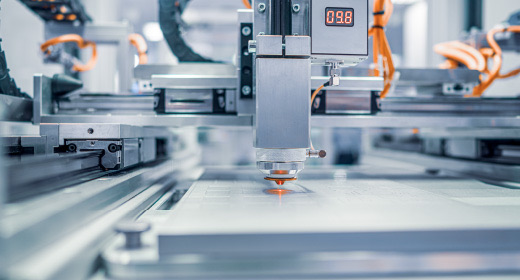
Advances in Solar Panel Materials
From the standard PV cells and thin-film technologies, solar panels continually evolve. Let's delve deeper into the more recent advances in solar panel materials.
Perovskite Materials
In the realm of photovoltaic technology, perovskite materials are gaining traction. These special solar materials don't require high temperatures for processing, offering an energy-efficient alternative to conventional cells. Possessing high light absorption and charge transport efficiency, perovskites enhance the performance of solar cells. For instance, according to the National Renewable Energy Laboratory (NREL), solar cells containing perovskite have achieved efficiency rates of over 25%.
Bifacial Solar Panels
Reinventing the solar industry, bifacial solar panels bring novelty and efficiency. These panels, constructed with dual-facing cells, capture sunlight from both sides. This double absorption mechanism allows them to generate up to 30% more electricity than traditional panels, as reported by the International Energy Agency (IEA). It's worth noting though; the increase in generation depends on the panel's mounting configuration and the reflectiveness of the surrounding surface. With innovation spearheading the solar panel industry, you can expect even more optimized and efficient solutions down the road.
Future Trends in Solar Panel Manufacturing
In light of the solar industry's continuous evolution, two notable trends are emerging: eco-friendly manufacturing practices and innovations in material efficiency.
Eco-Friendly Manufacturing Practices
Manufacturers increasingly incorporate green methods into their production lines, rooted in enhancing sustainability and reducing environmental footprint. For instance, firms like First Solar have successfully replaced the traditional energy-intensive process of creating crystalline silicon with thin-film Cadmium Telluride panels, leading to lower greenhouse gas emissions during production[^1^].
Moreover, recycling initiatives become more prevalent. PV Cycle in Europe is a prime example of a recycling program aiming to recover 85% of a solar panel's raw materials[^2^].
[1]: Source: "First Solar's Ecoefficiency program." First Solar.
[2]: Source: "PV Cycle Europe's recycling program." PV Cycle.
Innovations in Material Efficiency
The tireless pursuit of efficiency has brought about new material innovations. Silicon wafers, often used in Monocrystalline and Polycrystalline PV cells, are being gradually replaced with the introduction of perovskite cells. These new cells not only allow for energy-efficient processing but also reach high efficiency rates[^3^]. Bifacial solar panels have also emerged, being capable of generating up to 30% more electricity by capturing sunlight from both sides[^4^].
[3]: Source: "Perovskite Solar Cells: An overview." Solar Magazine.
[4]: Source: "Bifacial Solar Panels: A Comprehensive Guide." EnergySage.